
They are used at the tangent of the bend die to prevent tube material deformation. Wiper dies: Wiper dies are also insertions like mandrel, but they aren’t used inside the tube. Mandrel bending: Mandrel bending involves inserting a metal bar (called a mandrel) inside the tube during the bending process, so the tube does not collapse. To achieve the desired radius the process is repeated. The tube is then fed through the process by the driven rolls and bent in this way continuously. The rolls are often shaped to fit the tube diameter to prevent deformation of the cross-section. This causes plastic deformation, bending of the workpiece. An upper roll presses the tube down between the two rollers. The workpiece is placed on top of the two lower rolls. Roll bending can be classified further into 3-roll bending and 4-roll bending. There are many modifications to this method. Roll bending: In roll bending, a series of rollers push the pipe through a coil that is winding at the required bend angle. In this method, the pipe is clamped at both ends, and pressure is applied at the point where the bend is required. There are many different versions of rotary draw bending process.Ĭompression bending: Compression bending is an old-school bending method. In this method, the tube is clamped on its outer diameter and turned around a die called bend die. Rotary draw bending: Rotary draw bending is one of the best and most commonly used bending processes. While press bending is cheap, it doesn’t work on thick tubes. In press bending, two dies that are inclined at the required bend angle are pressed against a straight pipe to create the bend. Press or Ram bending: Press bending is one of the simplest bending processes. Below a brief overview of these different types. The major benefit of this method is that it provides higher accuracy, since there is no change in the final dimensions of the metal due to temperature changes.īesides this temperature-based classification of tube bending processes, the different types of tube bending can also be defined based on the technology used. The cold tube bending method does not require heating the metal tubing to a high temperature, the bending is accomplished at the room temperature of the tube.
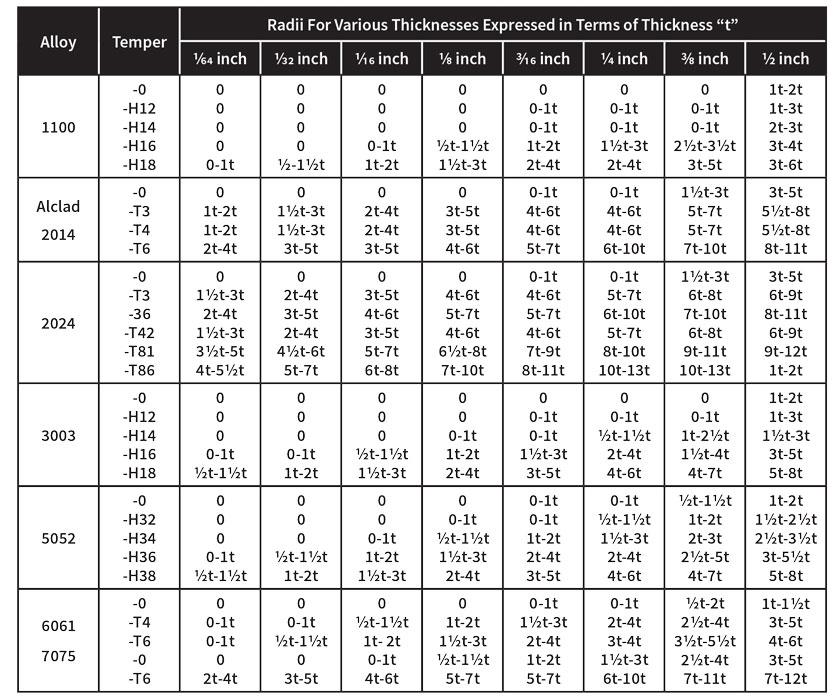
Metals at high temperatures become softer and flexible, so they don’t break and can bend with a lesser force.Ī major drawback of this method is that metals expand on heating, so the final dimensions of the bend and the angle of bend can be different on cooling than what is required. Pipe and Tube Bending Tube bending methods are mainly classified into two types - hot tube bending and cold tube bending.Īs the name suggests, hot tube bending involves heating the tube at a high temperature so the bending process becomes easier.
